Would you like to go to https://onsiter.com/us/ instead?
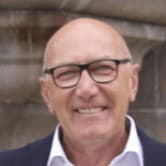
Peut être disponible
(Mis à jour 2023-10-05)Operations management
Helsingborg, Sverige
Natif Svenska, Serbian, Romanian, Moldavian, Moldovan, Courant English, Intermédiaire German
- Produktionsstyrning 30 års erfarenhet
- Förändrings ledning 20 års erfarenhet
- Ledarskap inom operations 30 års erfarenhet
Compétences (35)
COACHNING
REKRYTERING
OPTIMERING
Affärssystem
SCHEMALÄGGNING
Fabriksledningen
Förändrings ledning
PROCESSUTVECKLING
PROJEKTLEDNING
BEARBETNING
PRODUKTIONSPLANERING
TILLVERKNING
STYRNING
LEDARSKAPSUTVECKLING
VERKSTAD
Fabrikslayout
KAPACITETSPLANERING
OPERATIONS MANAGER
BUDGET
PROCESSTYRNING
PROJEKTLEDARE
MENTOR
Tillverkningsindustrin
SUPPLY CHAIN
SCANNING
ATT KÖPA/UPPHANDLING
KEMI
INKÖP
VÄXLA KAPACITET
Slipning
Formsprutning
VERKTYG
HYDRAULICS
RF
SVETSNING
Résumé
Are you looking for an experienced production manager/factory manager with long experience and documented results?
Below are results from my latest assignment at LSAB 2020, companies in the SEK 50m class
Efficiency savings SEK 2 million
Inventory value savings of SEK 2 million
Productivity +30% (85%)
Delivery +12% (97%)
Quality +50% (99%)
By:
- Implementation of daily management meeting
- KPI preparation and development
- Structure and order
- Factory layout change
- Picked up tools for production control
- Skill development/Education/flexibility
- Implemented an MPS system with scanning of TO
- Streamlining flow and processes
· Developed and optimized flow and processes
I am solution-oriented, efficient, structured and have the ability to quickly identify profits and opportunities, i.e. shortcomings and waste in the organization.
You get a senior, modern and experienced leader who has worked in several management positions in a number of different industries and companies within Operations such as COO, Operations Manager, Project Manager, Site Manager, Supply Chain Manager, Factory Manager and Production Manager.
In all my roles I have had personnel responsibility from 10 up to 50 employees and for 5 years I have worked as my own interim consultant.
I have very good skills and experience in all operational functions at a company and settle into the roles very quickly.
Is a non-prestige and action-oriented leader who works low and high and likes to roll up his sleeves and work on the production floor when necessary, and also takes an active role at a strategic level in a management team.
As a leader, I am fair, humble, transparent, straightforward, clear, honest, fearless, who with clear leadership engages and motivates the staff to change.
My competencies are in leadership, organizational development, change management, flow and process development, use of business systems, material management, warehouse management, capacity and production planning, production technology, production development and production layout.
Why you should hire me:
- has developed and optimized a number of companies/factories with very good results
- have all the tools I need and know what is required to succeed with the project
- solid experience and can easily find profitable changes
Expérience professionnelle
2022-10 - 2023-07
Project management Member of the company's management team Development of the company's KPI Warehouse management development Factory layout development Internal logistics, development Process development Optimize flow and processes.
Daily management development Production planning Process & development
2021-02 - 2022-09
Member of the company's Management Group Optimize flow and processes Operational purchase of machines and spare parts for 6 months Mentor to COC responsible and Warehouse Manager Development and optimization of cooperation with Welbilt China Ensure proper item data on Purchasing Items
2020-03 - 2020-11
2018-08 - 2020-02
2018-03 - 2018-06
2018-02 - 2018-02
2014-01 - 2018-02
Between 2014 and 2016, I transformed the plant into a profitable modern production unit.
The goal was to improve overall conditions to create a profitable business.
GOALS: * Decrease direct and indirect wage costs by 20% * Increase quality levels * Implement workplace health and safety risk management * Increase delivery security by 20% * Increase productivity by 20% GOALS SUBPROJECTS: * Employ MPS for production and capacity planning * Implement 5S * Implement daily control * Create tools for measuring KPI * Implement stock management system/material handling principles from warehouse to supplier * Reconfigure layout (stock and production) RESULTS: * Decreased direct and indirect wage costs by 23% * Decreased number of claims from 106 to 40 * Increased business risk management from 57% to 86% * Increased delivery accuracy to 99% * Increased productivity to 84% * Completed all subprojects RESPONSIBILITIES: * Accounting * Budget performance * Member of the company's management team (Nederman) * All staffing management (professional development, recruitment, etc.) * Employer representation in union matters
2016-04 - 2016-12
2016-04 - 2016-12
The goal was to create a modern manufacturing unit.
GOALS: * Decrease direct and indirect wage costs by 15% * Increase production area by 20% (approximately 1,000 sq.m.) via layout change GOALS SUBPROJECTS: * Implement MPS for production and capacity planning * Implement Shop Floor Control/Shop plan for staff on the production floor * Implement tools and methods for internal logistics RESULTS: * 1,000 sq.m. production area freed * 15% reduction in wage costs by June 2017 * All subprojects completed
2011-01 - 2013-01
The project's goal was a layout reconfiguration of the 2,500 sq.m. factory.
GOALS: * Free 20% of production space * Raise productivity by 10% GOALS SUBPROJECT: * Implement stock management system/principles from warehouse to supplier RESULTS: * 500 sq.m. of production space freed * 15% higher productivity * Stock management system/principles implemented
2006-01 - 2010-01
The assignment required relocation of manual machining, welding, and assembly, including * Pipe cutting, stainless steel and copper * Pipe bending, stainless steel and copper * Additional machining such as post-installation pipe flanging, sanding, grinding, and finishing * Welding, stainless steel and copper * Assembly stations with a high proportion of direct wages I worked from the beginning as a project manager, responsible for the relocation and establishment onsite.
Responsibilities included * Project leadership for relocating production from Sweden to Serbia * Geographical positioning in Serbia * Location search for approximately 600 sq.m.
* Establishing a contact network with banks, accountants, the municipality, the tax authority, and the customs authority * Coordinating all aspects of the relocation: staffing, layout, processes, professional development, organizational flow, and business system implementation * Logistics/shipping/inventory management of components and finished goods to and from Sweden * Establishing contacts and agreements with local suppliers and service providers RESULTS: After only six months, we delivered the first trailer of finished products from the newly established modern factory.
After the move, I was responsible for * Budget performance management * Operations management for all aspects of the business * Staff management (work procedures, routines/processes, selection criteria, and recruiting) * Production and capacity planning
2003-01 - 2006-01
Over a year, I increased productivity by 25% and reduced lead time from six to three weeks.
Among my responsibilities were stock management, capacity planning, production optimization, recruitment and professional development.
RESPONSIBILITIES: * Production/stock * Staff management * Production management * Work procedures, routines/processes, selection criteria, and recruiting * Production and capacity planning * Union negotiations * Delivery security to customer * Business systems development
2000-01 - 2003-01
Ecolux products (lighting fixtures) were previously manufactured by Samhall in Halmstad, Sweden.
Among my responsibilities were the factory layout, machine investment planning, flow processes, implementation of business systems, and staff recruitment.
RESPONSIBILITIES: * Production/stock * Staff management * Production management * Work procedures, routines/processes, selection criteria, and recruiting * Production technology * Production and capacity planning * Union negotiations * Delivery security to customer * Business systems development
1994-01 - 2000-01
RESPONSIBILITIES: * Production/stock * Budget performance management for the division * Member of the company's management team * Staff management * Production management * Work procedures, routines/processes, selection criteria, and recruiting * Production and capacity planning * Union negotiations
Parcours scolaire
1981-08 - 1984-06
Formations
1998-05
1998-06
2011-04
2017-06